Теория УЗК
Ультразвуковой контроль
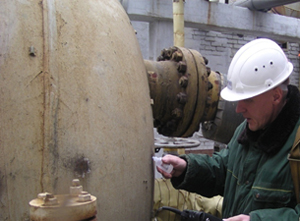
Объем применения УЗК как во многих отраслях промышленности нашей страны (энергетическое машиностроение, железнодорожный транспорт, судостроение, химическое машиностроение), так и за рубежом за последние годы достиг 70-80% по отношению к другим методам НК. Это объясняется более высокой чувствительностью (по раскрытию на 5 порядков) и лучшей выявляемостью трещиноподобных дефектов, более высокой оперативностью (15-20 раз) и производительностью (2-4 раза), меньшей стоимостью (2-6 раз) и безопасностью в работе по сравнению с традиционными методами радиографического контроля.
Ультразвуковая дефектоскопия как самостоятельная область науки зародилась в СССР. Датой рождения акустических методов контроля считается 2 февраля 1928г. В этот день Комитет по делам изобретений получил заявку преподавателя ЛЭТИ С.Я.Соколова на способ и устройство для испытания материалов. С середины 1950-х годов этот прогрессивный метод НК материалов активно применяется для оценки качества продукции.
Ультразвуковая толщинометрия
Принцип ультразвуковой толщинометрии основан на измерении времени прохождения ультразвукового импульса в изделии и умножении измеренного времени на коэффициент, учитывающий скорость звука в материале изделия.
Рассмотрим данный процесс по этапам:
1. Прибор генерирует ультразвуковой импульс.
2. Ультразвуковой импульс, излучаемый преобразователем, передаётся к поверхности объекта контроля.
3. Импульс проникает в объект контроля.
4. Импульс проходит до противоположной поверхности и отражается от неё.
5. После этого импульс возвращается обратно к преобразователю через материал объекта контроля.
6. Ультразвуковой импульс передаётся от поверхности объекта контроля в преобразователь.
7. Принятый отражённый импульс измеряется прибором.
Для получения достоверных результатов при рассмотрении представленных этапов необходимо следующее:
1. Создание ультразвукового импульса. Пьезоэлемент, возбуждаемый очень коротким (<1 мкс) электрическим импульсом, излучает ультразвуковой сигнал. Для получения возможности точного измерения данного сигнала, длина волны импульса должна быть максимально короткой, т.е. частота должна быть максимально высокой. В большинстве случаев для толщинометрии используется ультразвук в диапазоне частот от 1 до 20 МГц. Стандартное значение частоты составляет 5 МГц, что соответствует длине ультразвуковой волны в стали около 1 мм.
2. Ввод ультразвукового импульса в металл объекта контроля. Поверхность металла должна быть в достаточной степени гладкой и чистой. На поверхности не должны присутствовать препятствия мешающие прохождению ультразвуковой волны, такие как рыхлые продукты коррозии и отслоившееся ЛКП, которые подлежат удалению. Не допускается наличие воздушного зазора между излучающей поверхностью ПЭП и поверхностью объекта контроля. Ультразвук плохо распространяется по воздуху в связи с чем применяется контактная жидкость, такая как минеральное масло, вода или гель, которые обеспечивают хороший акустический контакт.
3. Ультразвуковой импульс распространяется в структуре объекта контроля. Большинство металлов являются хорошими проводниками звука. При УЗК высококачественного металлопроката и стальных поковок с мелкозернистой структурой ультразвук распространяется на расстояние в несколько метров. Контроль некоторых материалов, однако, не является столь простой задачей. Литейный чугун имеет крупнозернистую структуру, которая не очень хорошо проводит ультразвук. Неоднородные материалы, такие как пластмасса, армированная стекловолокном, могут создавать трудности при УЗК. Отдельные пористые материалы не дают отражения ультразвука, в то время как другие могут многократно отражаться в структуре материала, давая ложные показания толщины. Для толщинометрии сложных материалов следует использовать низкочастотные преобразователи несмотря на их низкую чувствительность. Большое значение имеет также постоянство скорости распространения УЗК в материале. Если данная скорость варьируется, то точность измерения расстояния будет соответствующим образом уменьшена.
4. Ультразвуковой импульс отражается от дальней стенки объекта. Плоские параллельные поверхности обеспечивают хорошее отражение ультразвука. Непараллельные поверхности могут отражать ультразвук в сторону от рабочей поверхности ПЭП (см. рисунок). Шероховатые поверхности рассеивают ультразвук и лишь часть его возвращается назад к ПЭП, что в результате ослабляет сигнал.
5. Принятие отражённого ультразвукового сигнала и его измерение. Другой (а иногда и тот же самый) пьезоэлектрический кристалл используется для приёма ультразвука, который преобразуется в электрический импульс с последующим измерением времени. При наличии достаточно сильного отражённого сигнала главной проблемой являются помехи от передавемого импульса. Как правило, результатом этого является время задержки после отправки зондирующего импульса. Для обхода данного ограничения выполняется задержка принимаемого сигнала с учётом толщины пластмассовой линии задержки.
Прочие факторы влияющие на результаты ультразвуковой толщинометрии
Температура. Чем выше температура, тем ниже скорость распространения ультразвука в материале. Поскольку скорость ультразвука меняется вместе с температурой большое значение имеет калибровка толщиномера при той же самой температуре, что и температура измеряемого материала.
Высокая температура может привести к повреждению ПЭП и создаёт проблемы с использованием различных контактных жидкостей. В основном типовые ПЭП способны работать при температуре около 80°С. При измерениях выше данной температуры необходимо использовать специальные ПЭП оснащённые линиями задержки изготовленные из жаропрочных материалов. В зависимости от величины температуры требуется периодическое охлаждение ПЭП.
Стандартный ультразвуковой контактный гель на водной основе будет быстро высыхать при высокой температуре и станет непригодным при той же самой температуре, что и типовые ПЭП. Выпускается ассортимент контактных жидкостей для выполнения измерений при высокой температуре.
Поправка на V-схему хода лучей раздельно/совмещенного ПЭП
Измерение толщины на изогнутых поверхностях. При измерении толщины на крутоизогнутых поверхностях (например, на трубном прокате) раздельно-совмещённым преобразователем его рабочая поверхность должна располагаться так, чтобы акустический экран был поперек продольной оси трубы.
Измерение толщины через покрытия в режиме эхо-эхо. При измерении толщины изделий с поверхностными покрытиями следует с осторожностью оценивать полученные показания. Отслоившиеся или неравномерные покрытия могут значительно ослаблять ультразвуковой сигнал и обычно они подлежат удалению. Даже покрытия с хорошей адгезией, которые не препятствуют распространению ультразвука, создают дополнительную задержку. Обычно скорость распространения ультразвука в слое ЛКП составляет от трети до половины значения скорости в стали. Типовой слой ЛКП толщиной 200 мкм даст увеличенное на 0,5 мм показание толщины. Если требуемый уровень точности не слишком высок, а толщина слоя ЛКП равномерна, то можно просто вычесть соответствующую поправку, но данное решение редко является удовлетворительным.
Наилучшим подходом к решению данной задачи является измерение положения первого и второго эхосигналов. Поскольку ультразвук один раз проходит через слой ЛКП и отражается внутри изделия из стали, то оба эхосигнала будут иметь одинаковую задержку, т.е. путём измерения разности времени между двумя эхосигналами можно получить точное значение толщины металла, на которое не влияют изменения толщины слоя ЛКП (см. рисунок). Однако следует заметить, что в случае сильно корродированной задней стенки отсутствует возможность измерить второй эхосигнал по причине его значительного ослабления.
Типы ПЭП используемых для толщинометрии
Необходимо заметить, что ПЭП общего назначения используемые для оценки степени коррозионного разрушения являются раздельно-совмещёнными. Толщиномеры используемые для точного измерения толщины используют с прямыми совмещёнными ПЭП, обычно оснащёнными линией задержки. Большинство специализированных толщиномеров работают как с совмещёнными, так и с раздельно-совмещёнными ПЭП, но лишь немногие модели рассчитаны на работу с ПЭП обоих типов.
Раздельно-совмещённые ПЭП
- Возможность работы с простой элементной базой прибора. Разделены функции излучения и приёма сигнала, могут использоваться простые усилители без перегрузки генератора импульсов. Управляемое изменение параметров контроля в соответствии с расстоянием, достаточно простая автоматическая регулировка усиления (АРУ).
- Хорошо подходят для контроля изделий с шероховатой поверхностью, а также для поиска язвенной коррозии, пористости и небольших дефектов.
- Требуется внесение поправки на V-схему хода лучей. Разделение элементов значительно снижает чувствительность при контроле тонкостенных материалов. Практически измеряемая минимальная толщина составляет около 1 мм.
Совмещённые ПЭП с линией задержки
- Прямой путь хода ультразвукового луча – не требуется внесение поправки на V-схему хода лучей. Пригодны для контроля тонкостенных материалов (вплоть до толщины около 0,2 мм).
- Внутреннее переотражение сигнала ограничивает максимально полезную измеряемую толщину материала временем равным длине линии задержки, которая обычно равна 25 мм.
- Стандартно поставляются со сменными призмами, могут комплектоваться притертыми призмами для контроля искривлённых поверхностей.
Совмещённые ПЭП
- Прямой путь хода ультразвукового луча.
- Низкая околоповерхностная чувствительность из-за времени задержки после зондирующего импульса. Могут использоваться для контроля изделий с минимальной толщиной стенки около 3 мм.
- Отсутствие задержки отражённого сигнала позволяет использовать ПЭП в широком диапазоне частот.
- Сила ультразвукового импульса значительно ослабляется при контроле с большого расстояния, что зачастую требует ручной настройки усиления и применения стробирования.
- Стандартно выпускаются с твёрдой рабочей поверхностью стойкой к износу.
- Обыкновенно используются с одноэлементными толщиномерами для контроля толстостенных материалов.
Ультразвуковая дефектоскопия
Дефектоскоп предназначен для поиска, определения координат и оценки размеров различных нарушений сплошности и однородности материала в изделиях из металлов и композитов. Дефектоскоп обеспечивает реализацию типовых и специализированных методик УЗ НК сварных швов, позволяет выполнять УЗ толщинометрию и дефектоскопию широкого класса изделий, вести поиск мест коррозии, трещин, внутренних расслоений и других типов дефектов.
Типовыми областями применения прибора является НК сварных швов трубопроводов, котлов, металлических конструкций при производственном, сборочном и эксплуатационном контроле на предприятиях нефтегазового комплекса, в энергетике, транспорте, судостроении, авиакосмической отрасли и т.д.
Реализуемые методы контроля
Дефектоскоп поддерживает следующие методы ультразвукового контроля:
- Эхоимпульсный метод
- Теневой метод
- Контактный или иммерсионный методы
- Контроль наклонным преобразователем (поперечная волна)
- Контроль наклонным преобразователем (поверхностная волна)
- Методы TOFD, основанные на дифракции УЗ волны на трещине
- Измерение координат дефекта
- Толщинометрия совмещенным преобразователем
- Толщинометрия раздельно-совмещенным преобразователем
- Измерение скорости ультразвука в материале
- Измерение времени распространения в микросекундах
- Методы, основанные на изменении фазы радиосигнала
- Контроль по методу «тандем»
Для точной дефектоскопии требуется соблюдение трех условий:
- Выбор подходящего преобразователя.
- Хороший эталонный образец, изготовленный из того же материала, что и объект контроля, и имеющий искусственные дефекты различной ориентации, имитирующие при заданной чувствительности реальные дефекты.
- Правильная настройка рабочих параметров дефектоскопа.
Преобразователи, используемые для дефектоскопии, обычно бывают узкополосными для обеспечения наилучшей чувствительности к несплошностям. В некоторых случаях используются широкополосные преобразователи для оптимизации разрешения у ближней или дальней поверхности объекта и, как следствие, наличия возможности различать, из какой зоны получен эхосигнал. Выбор частоты осуществляется таким образом, чтобы длина волны в материале была оптимальной для выявления дефектов требуемого размера и ориентации. В основном, применяются прямые совмещённые, а также наклонные преобразователи для выявления дефектов в сварных швах. Имеются также специальные раздельно-совмещенные преобразователи и преобразователи поверхностной волны.
Следующим важным условием для точной дефектоскопии является стандартный образец. Данный образец изготавливается из материала ОК и должен иметь ту же скорость ультразвуковой волны и характеристики затухания. Поверхность стандартного образца должна имитировать поверхность объекта контроля, чтобы характеристики затухания и чувствительности были сходными. Стандартный образец должен иметь ряд искусственных дефектов, эквивалентных по размеру и ориентации тем, которые должны быть выявлены в процессе контроля. Это могут быть плоскодонные отверстия, просверленные перпендикулярно или параллельно поверхности, пропилы, зарубки. Должны также иметься искусственные дефекты, расположенные у ближней и дальней поверхности образца для определения разрешающей способности комбинации параметров преобразователя и дефектоскопа.
Для качественной дефектоскопии, необходимо выполнить точную настройку рабочих параметров (калибровку) дефектоскопа. Необходимо выполнить настройку генератора, усилителя и параметров строба таким образом, чтобы обеспечить необходимую чувствительность и разрешающую способность.
Контроль сварных швов
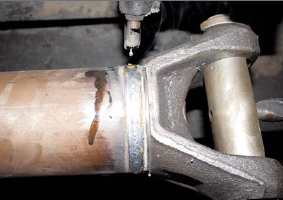
Прибор определяет координаты дефектов в сварных соединениях с помощью наклонных преобразователей. Используется возможность дефектоскопа рассчитывать расстояние до дефекта по поверхности и глубину дефекта, исходя из измеренной удаленности по лучу. Точность измерений достигается путем точного задания угла ввода ультразвука в материал. Дополнительно, в случае контроля отраженным лучом, требуется ввести общую толщину объекта контроля. Измерения выполняются по приведённой ниже схеме.
Значения измерений отображаются в нижней части экрана:
Расстояние по лучу B от точки ввода преобразователя до дефекта, равное сумме В1 и В2 при контроле отраженным лучом. Расстояние S от точки излучения преобразователя до проекции дефекта на поверхность объекта контроля. При вводе расстояния от передней грани преобразователя до точки излучения (осуществляется в меню ДАТЧИК (PROBE)), на дисплее в качестве расстояния S отображается укороченное расстояние от передней грани ПЭП до проекции дефекта на поверхность. Глубина D залегания дефекта.Пример отображения информации на дисплее.
Информация о размере дефектов отображается с правой стороны строки в %, Дб, или значения эквивалентного диаметра отражателя. В приведённом выше примере амплитуда эхосигнала представлена в виде процентной величины от полной высоты экрана и составляет 85%. При запуске функции ДАК (DAC) оператор может включить индикацию в дБ, в % от полной высоты экрана или от уровня кривой ДАК. При использовании метода АРД (DGS/AVG) с правой стороны отображаются значения эквивалентного диаметра отражателя.
На примере эквивалентный диаметр дефекта составляет 4,2 мм.
Важно помнить, что дефекты в сварных соединениях могут быть как точечными, так и протяженными. Поэтому хорошие результаты контроля могут быть достигнуты, если прибор тщательно настроен, и оператор внимательно следит за пиком эхосигнала на дисплее.
Толщинометрия
Для правильного измерения толщины требуется соблюдение трех условий:
а) Правильный выбор преобразователей.
б) Стандартный образец, изготовленный из материала объекта контроля.
в) Точная настройка дефектоскопа.
Для измерения толщины используются три типа прямых преобразователей, излучающих продольную волну. Контактные совмещенные преобразователи используются для измерений, когда ожидаемая толщина объекта контроля превышает 2,5 мм. Преобразователи с линией задержки используются для измерений толщины тонких объектов с толщиной от 0,5 мм, при этом поверхности должны быть чистыми и параллельными.
Раздельно-совмещенные преобразователи могут быть использованы для измерения толщины достаточно тонких объектов (от 1 мм), при этом поверхности объекта контроля могут быть шероховатыми и не обязательно параллельными. Раздельно-совмещенные преобразователи широко используются для измерения толщины корродированных объектов. Однако излучающий и принимающий элементы раздельно-совмещенных преобразователей расположены под небольшим углом друг к другу, что вызывает небольшую нелинейность измерений. В связи с этим требуется калибровать и использовать их в ограниченном диапазоне измерений.
Вне зависимости от типа используемого преобразователя, важно, чтобы он был разработан специально для толщинометрии. Это означает, что они должны быть широкополосными или сильно-демпфированными, иными словами, должны иметь короткий передний фронт. В противном случае, амплитудные вариации сигналов могут вызвать полуволновые ошибки.
Следующим требованием для точного измерения толщины является калибровка или наличие стандартного образца. Этот образец изготавливается из материала объекта контроля. Другими словами, он должен иметь ту же скорость и характеристики затухания, что и объект контроля. Стандартный образец должен иметь как минимум две параллельные поверхности, расположенные на расстояниях, соответствующих минимальной и максимальной толщине объекта контроля. Желательно, чтобы образец имел четыре секции с различной толщиной, находящейся в диапазоне контроля.
Допускается проведение настройки дефектоскопа по одной точке, используя стандартный образец только с одним известным значением толщины. Это менее желательная методика, так как она не дает возможности в варьировании настройки. При настройке по этой методике сначала определяется ноль преобразователя на образце из другого материала, имеющего три или четыре секции с известной толщиной, а затем значение скорости, установленное в дефектоскопе, регулируется в процессе измерения известной толщины контрольного образца. Таким образом, выставляется точная скорость ультразвука.
И, наконец, требуется провести настройку прибора для выполнения точных измерений толщины. Для этого требуется установить параметры генератора и усилителя таким образом, чтобы эхоимпульсы имели острый передний фронт.