ПРИМЕНЕНИЕ УЛЬТРАЗВУКОВОЙ СИСТЕМЫ RS 2 WP ДЛЯ ОТРАБОТКИ УЛЬТРАЗВУКОВОГО КОНТРОЛЯ ЛИСТОВ И ПЛИТ ИЗ АЛЮМИНИЕВОГО СПЛАВА АМг6 И УГЛЕПЛАСТИКА
МИЛЬЯЧЕНКО Александр Александрович
Инженер-технолог 2-й категории, ФГУП «НПО «Техномаш», Москва
ВИННИК Ирина Евгеньевна
Инженер-технолог 1-й категории, ФГУП «НПО «Техномаш», Москва
СЕМЕРЕНКО Алексей Владимирович
Руководитель отдела средств НК и ТД, специалист III уровня по УЗК, ООО «Панатест», Москва
Журнал "Территория NDT", апрель-июнь, 2015.
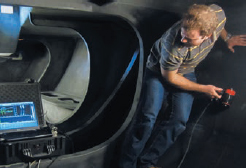
Рис. 1. Контроль металлов и композитов.
Целью данной работы являлась отработка ультразвукового контроля (УЗК) листов и плит из сплава АМг6 и композитного материала (рис. 1) на основе углеродных волокон для определения размеров и координат искусственных дефектов, а также основных параметров УЗК – предельной чувствительности, фронтальной и лучевой разрешающей способности, мертвой зоны.
Для исследований использовали ультразвуковой дефектоскоп RS 2 WP производства Sonatest, Великобритания (рис. 2). Прибор разработан для высокоскоростного линейного сканирования больших площадей с применением технологии фазированных решеток (ФР) и получением A-, B- и С-сканов в реальном масштабе времени. Типовые области применения дефектоскопа включают в себя контроль металлов и композитных материалов на основе углеродных волокон, выявление таких дефектов, как расслоения, трещины, дефекты поверхности, коррозия, газовые поры, включения инородных материалов, контроль целостности клеевых соединений.
Основные технические характеристики системы RS 2 WP
Ширина полосы пропускания, Гц ...................... 1–22
Амплитуда генератора зондирующих импульсов, В ........................................ 70
Максимальное число каналов ............................... 128
Число активных каналов ....................................... до 32
Количество измерительных стробов .................... до 6
Количество С-сканов, получаемых одновременно ........................................ до 4
Получение А-, В-, С-сканов в реальном времени, функция построения карт больших площадей (сшивка),
Программные средства для автоматической оценки параметров дефекта
RS 2 WP является многоканальным ультразвуковым дефектоскопом, использующим матричный роликовый преобразователь (рис. 3) с линейным расположением элементов по ширине ролика, для контроля больших участков поверхности.
|
|
Эта универсальная система ликвидирует разрыв между ручным и стационарным оборудованием, обес печивая удобство и универсальность портативного прибора в сочетании со скоростью и возможностью углубленного анализа данных автоматизированной системы контроля. По сравнению с другими приборами ультразвукового контроля дефектоскоп RS 2 WP способен выполнять сканирование и обработку данных на порядок быстрее, обеспечивая при этом высочайшую точность получаемых результатов.
Скорость перемещения роликового преобразователя WP может варьироваться в интервале 3…400 мм/с, что при рабочей длине матрицы ФР 50 мм эквивалентно скорости контроля 1м2/мин, а при длине 100 мм – 2 м2/мин. Важным достоинством измерительной системы RS 2 WP по сравнению с аналогичными системами с ФР являются простота настройки и работы с прибором.
Габариты имитаторов дефектов, выполненных в образце-плите размером 540×150×15 мм из сплава АМг6
Группа |
Диаметр отверстия, мм |
Глубина отверстия, мм |
Примечание |
I |
4 |
7 |
Вертикальное цилиндрическое отверстие |
3 |
6 |
Вертикальное цилиндрическое отверстие |
|
II |
3 |
50 |
Боковое цилиндрическое отверстие |
III |
4 |
7 |
Вертикальное цилиндрическое отверстие |
IV |
3 |
5 |
Вертикальное цилиндрическое отверстие |
4 |
7 |
Вертикальное цилиндрическое отверстие |
|
3 |
8 |
Вертикальное цилиндрическое отверстие |
|
3 |
7 |
Вертикальное цилиндрическое отверстие |
|
V |
4 |
7 |
Вертикальное цилиндрическое отверстие |
Основные параметры настройки ультразвуковой системы RS2WP для контроля плит
(опыт № 1)
Усиление, дБ ...................................................................................................... 50
Глубина А-скана, фиксируемая и выводимая на экран, мм ............................ 22,9
Задержка начального положения вывода А-скана с преобразователя, мм ..... 104,5
Частота генератора, кГц ..................................................................................... 5,0
Скорость ультразвука в материале, м/c ............................................................ 6300
|
|
|
|
|
|
|
|
Рис. 6. Выявление имитаторов дефектов в виде вертикального (а,в,г,д) и бокового (б) цилиндрического отверстия (А-, В- и С-сканы): |
Основные параметры настройки ультразвуковой системы RS2WP для контроля листов
(опыт № 2)
Усиление, дБ ...................................................................................................... 50
Глубина А-скана, фиксируемая и выводимая на экран, мм ............................ 8,2
Задержка начального положения вывода А-скана с преобразователя, мм ..... 104,7
Частота генератора, кГц ..................................................................................... 5,0
Скорость ультразвука в материале, м/c ............................................................ 6300
|
|
|
|
|
|
|
|
Рис. 9. Выявление имитаторов дефектов в виде вертикального цилиндрического отверстия диаметром (А-, В- и С-сканы): |
Основные параметры настройки ультразвуковой системы RS2WP для контроля листов
(опыт № 3)
Усиление, дБ ...................................................................................................... 50
Глубина А-скана, фиксируемая и выводимая на экран, мм ............................ 3,3
Задержка начального положения вывода А-скана с преобразователя, мм ..... 49,5
Частота генератора, кГц ..................................................................................... 5,0
Скорость ультразвука в материале, м/c ............................................................ 2870
|
|
|
|
|
|
Рис. 12. Выявление имитаторов дефектов в виде плоскодонного отверстия диаметром (А-, В- и С-сканы): |
Опыт № 1
Отработку УЗК на ультразвуковой системе RS 2WP проводили на об раз це-плите размером 540×150×15 мм из сплава АМг6, в котором были выполнены сверления с плоским дном, имитирующие расслоения (группы I, III, IV, V), и боковое цилиндрическое отверстие (группа II), имитирующие объемные дефекты (рис. 4), габариты которых представлены в таблице. Схема контроля образца ультразвуковой системой RS 2 WP представлена на рис. 5. Результаты УЗК представлены в виде А-, В- и С-сканов на рис. 6.
Опыт № 2
Для второго опыта отработку УЗК проводили на образцелисте размером 540×150×6 мм из сплава АМг6 с имитаторами расслоения в виде вертикальных цилиндрических отверстий диаметром 6, 5, 4, 3, 2 мм на глубине 3 мм (рис. 7).
Схема контроля образца ультразвуковой системой RS2WP представлена на рис. 8. Результаты отработки ультразвукового метода контроля представлены в виде А-, В- и С-сканов на рис. 9.
Опыт № 3
Для отработки УЗК углепластиковых листов использовали образец № 3 (рис. 10), который представляет собой пластину размером 202×97×2,4 мм. В образце выполнены имитаторы расслоения, представляющие собой несквозные плоскодонные отверстия с одной (тыльной) стороны образца с диаметрами 6, 4, 3 мм, расположенные на расстоянии 30 мм друг от друга и глубиной 1,97 мм. Схема контроля ультразвуковой системой RS 2 WP представлена на рис. 11.
Результаты экспериментов представлены в виде А-, В- и С-сканов на рис. 12.
Выводы
1. Во всех трех опытах с помощью системы RS 2WP надежно выявлены все искусственные отражатели в образцах как из алюминиевого сплава, так и из углепластика.
2. В результате опытов получены следующие результаты:
• предельная чувствительность на алюминиевых плитах не хуже 3,14 мм2 (опыт № 2);
• предельная чувствительность на углепластике не хуже 7 мм2 (опыт № 3);
• лучевая разрешающая способность на алюминиевых плитах не хуже 1 мм (опыт № 1);
• фронтальная разрешающая способность на алюминиевых плитах не хуже 1 мм (опыт № 1);
• мертвая зона на углепластиковом листе не более 0,43 мм (опыт № 3).
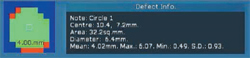
Рис. 13. Информация о дефекте, полученная с помощью ультразвуковой системы RS 2 WP.
3. Получены результаты в виде А-, В- и С-сканов, по которым с высокой точностью определены размеры и глубина залегания отражателей. Площадь отражателей рассчитывалась автоматически. Для этого выделяли площадь дефекта одним из предлагаемых типов контура в виде круга, эллипса, прямоугольника или многоугольника. Тогда в текстовом поле «Информация о дефекте» отображались статистические данные, автоматически рассчитанные системой: координаты, площадь, текущее значение глубины, а также среднее, максимальное, минимальное значения глубины в пределах выделенного контура (рис. 13).
4. Выявление и интерпретация дефектов упрощаются с помощью данных С-скана. После регистрации несколько С-сканов могут быть собраны в единый мозаичный Т-скан. В собранном Т-скане имеется возможность добавления, перемещения и разворота отдельных С-сканов в целях их компоновки. Имеется возможность сохранения, экспорта и печати сканов в виде масштабированных изображений или изображений в натуральную величину с раскладкой на несколько страниц для последующего наложения на деталь и точного определения местоположения дефектов.
5. Возможна разработка методики ультразвукового метода контроля плит на ультразвуковой системе RS 2 WP.