УЛЬТРАЗВУКОВОЙ КОНТРОЛЬ ИЗДЕЛИЙ ИЗ КОМПОЗИЦИОННЫХ МАТЕРИАЛОВ, ПРИМЕНЯЮЩИХСЯ В АВИАСТРОИТЕЛЬНОЙ ОТРАСЛИ ПРОМЫШЛЕННОСТИ
СЕМЕРЕНКО Алексей Владимирович
Руководитель отдела средств НК и ТД, специалист III уровня по УЗК, ООО «Панатест», Москва
Журнал "Территория NDT", октябрь-декабрь, 2014.
В современном авиастроении наряду с традиционными алюминиевыми сплавами все большее применение находят полимерно-композиционные материалы (ПКМ), которые увеличивают прочность деталей, снижают их массу и подверженность коррозии.
Очевидно, что с повышением востребованности многослойных композитов ужесточаются требования к их диагностике. В связи с этим необходимо изучение свойств этих материалов и выявление возможных типов дефектов.
Дефекты в деталях самолетов и вертолетов из ПКМ можно разделить на две группы: внутренние дефекты и дефекты соединения. Внутренние дефекты представляют собой расслоения, трещины, поры, деформацию от ударов, а к дефектам соединения относятся повреждения клеевого слоя.
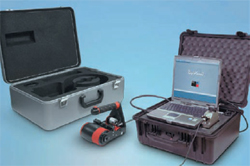
Рис. 1. Дефектоскоп RS 2 WP.
В настоящее время самым перспективным методом акустического вида неразрушающего контроля (НК) для выявления дефектов из ПКМ является эхоимпульсный метод, поскольку при одностороннем доступе к объекту контроля (ОК) позволяет определять размеры дефектов, координаты и их характер.
Основной сложностью при контроле изделий из ПКМ является сильное затухание ультразвука, связанное со сложной структурой материала. Также контроль осложняют неровности поверхности ПКМ.
Для высокоскоростного линейного сканирования больших площадей композитов компания Sonatest (Великобритания) предлагает ультразвуковой дефектоскоп RS 2 WP (рис. 1), в котором применяются технологии фазированных решеток и получения А-, В- и С-сканов в реальном времени.
Прибор состоит из блока сбора информации, промышленного ноутбука для обработки результатов и роликового преобразователя.
Основные технические характеристики системы RS 2 WP
Ширина полосы пропускания, Гц ...................... 1–22
Амплитуда генератора зондирующих импульсов, В ........................................ 70
Максимальное число каналов ............................... 128
Число активных каналов ....................................... до 32
Количество измерительных стробов .................... до 6
Количество С-сканов, получаемых одновременно ........................................ до 4
Получение А-, В-, С-сканов в реальном времени, функция построения карт больших площадей (сшивка),
Программные средства для автоматической оценки параметров дефекта
Одной из особенностей описываемой системы RS 2 WP является роликовый преобразователь (РП) с фазированной решеткой (ФР). РП идеально подходит для ручного контроля больших плоских или криволинейных поверхностей. Подпружиненный ролик создает постоянное прижатие преобразователей к контролируемой поверхности при сканировании даже узких деталей различной пространственной ориентации.
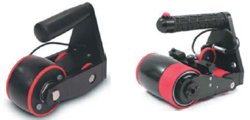
Рис. 2, 3. Одноэлементный РП (слева). РП с ФР (справа).
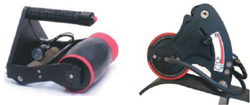
Рис. 4, 5. РП с ФР для широких ОК (слева). РП для работы по радиальным поверхностям (справа).
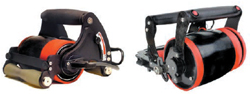
Рис. 6, 7. РП для получения карты коррозии (слева). РП низкой частоты (справа).
Резиновый протектор обеспечивает акустический контакт с поверхностью ОК и получение точных данных без необходимости использования контактного геля или большого количества воды. Износостойкая резиновая шина подходит для неровных поверхностей (параметр шероховатости ~1 мм).
Рассмотрим несколько моделей РП, разработанных для применения с системой RS 2 WP.
Одноэлементный РП (рис. 2). В нем используется одиночный 15-миллиметровый иммерсионный ПЭП, предназначенный для работы на частотах 1, 2, 5, 10 МГц. Датчик оснащен оптическим измерителем линейного расстояния. Может быть подключен к дефектоскопу MasterScan, Sonatest.
РП с ФР (рис. 3) – запатентованный датчик, являющийся результатом совместных исследований Sonatest с авиационными предприятиями. Этот прибор идеально подходит для ручного сканирования плоских и малоизогнутых объектов, позволяет значительно повысить производительность контроля. Частота 2, 5, 10 МГц, количество элементов 64, активная зона 45 мм.
РП с ФР для широких ОК (рис. 4) может сканировать изогнутые части с помощью регулировки угла наклона ФР к поверхности ОК. Используя более широкую шину, такой РП позволяет достичь вдвое большую производительность контроля. Количество элементов 128, активная зона 96 мм.
Для работы по радиальным поверхностям предназначен РП (рис. 5) с регулировкой угла наклона решетки с помощью рычага, расположенного на боковой поверхности датчика. Минимальный диаметр кривизны поверхности контроля составляет 10 см. Благодаря дополнительной конструкции переднего ролика подходит и для продольного сканирования. Обеспечивает обнаружение едва видимых повреждений композитных материалов в аэрокосмической и машиностроительной отраслях.
РП для получения карты коррозии (рис. 6) имеет эргономичный дизайн. РП, разработанный для контроля сосудов и трубопроводов, облегчает проведение диагностики объектов с цилиндрической поверхностью за счет хорошей фиксации ролика на поверхности. Благодаря заполненной жидкостью шине датчик подходит для контроля грубых, ржавых поверхностей. Количество элементов 64, активная зона 44,8 мм.
РП низкой частоты (рис. 7) разработан специально для контроля протяженных объектов из композитных материалов с высокой степенью затухания, таких как, например, стеклопластик толщиной до 60 мм. Частоты 0,5 или 1 МГц, количество элементов 50, активная зона 85 мм.
Производительность контроля при использовании РП с решеткой из 64 и 128 элементов приведена в таблице.
Производительность контроля при использовании РП
Параметр | Количество элементов решетки РП | |||
64 | 64 | 128 | 128 | |
Разрешение сканирования, мм | 0,8×0,8 | 1,6×1,6 | 0,8×0,8 | 1,6×1,6 |
Производительность: при линейном сканировании, мм/с | 200 | 800 | 200 | 800 | при сканировании площади, м2/мин | 0,5 | 2 | 1 | 4 |
Убедиться в эффективности описанной системы помогут несколько примеров.
Контроль расслоений
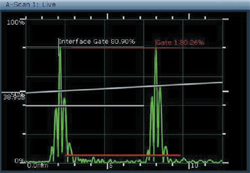
Рис. 8. Настройки измерительных стробов.
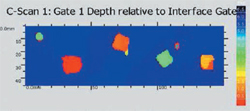
Рис. 9. C-скан шести расслоений.
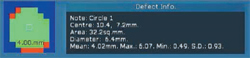
Рис. 10. Информация о дефекте для контура «Круг».

Рис. 11. Контроль пористости по изменению амплитуды донного сигнала.
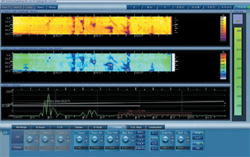
Рис. 12. Одновременное отображение С-скана 1 и С-скана 2.
Пример поиска расслоений диаметром более 5 мм рассмотрим на образце из углепластика толщиной 6 мм. Контроль ведется на частоте 5 МГц. Скорость звука в ОК 3075 м/с.
Временная регулировка чувствительности (ВРЧ) настраивается так, чтобы эхосигналы от поверхности ввода и донной поверхности имели одинаковую амплитуду. Измерения проводят по времени прихода донного сигнала относительно интерфейсного сигнала (рис. 8).
Карта цветов для получения C-скана настраивается на охват всего диапазона данных по глубине. Выбираем специальную цветовую схему Spectrum: 0 мм (красный) – 7 мм (синий). Проводим сканирование образца. Полученный C-скан с шестью расслоениями приведен на рис. 9.
Глубина каждого дефекта представлена соответствующим цветом и показывает возможности контроля как подповерхностной, так и донной областей.
Для получения информации о дефекте необходимо выделить его площадь одним из предлагаемых типов контура в виде круга, эллипса, прямоугольника или многоугольника.
Тогда в текстовом поле «Информация о дефекте» отобразятся статистические данные, автоматически рассчитанные системой: координаты расслоения, площадь, текущее значение глубины, а также среднее, максимальное, минимальное значения глубины в пределах выделенного контура (рис. 10).
Контроль пористости
Данный пример демонстрирует использование дефектоскопа RS 2 WP для поиска пористости, небольших пустот и инородных включений в образце из углепластика переменной толщины 4–8 мм с одновременным контролем разнотолщинности образца.
Контроль пор, особенно небольших размеров, – традиционно непростой вопрос для УЗД. Поэтому для более надежного выявления пор рассмотрим два способа контроля пористости: по отражению сигнала непосредственно от поры и по уменьшению амплитуды донного сигнала – затуханию.
ВРЧ настраивается так же, как для контроля расслоения. Хотя лучше настраиваться на образце, изготовленном из углепластика и содержащем несколько небольших (около 2 мм) плоскодонных отверстий на разной глубине.
Сначала рассмотрим вариант контроля по уменьшению амплитуды донного сигнала. Выбираем специальную цветовую схему Aerospace. Настраиваем карту цветов по амплитуде: 0 % черный – лиловый – оранжевый – желтый – белый и записываем C-скан 1, отображающий изменение амплитуды донного сигнала (рис. 11).
Полученный C-скан 1 информативен для обнаружения микропористости. Для контроля пористости по отражению настраиваем второй измерительный строб. Здесь используем возможности RS 2 WP по применению измерительных стробов переменной ширины. Начинаться второй строб должен как можно ближе к интерфейсному сигналу, а заканчиваться как можно ближе к донному сигналу.
Карта цветов устанавливается, как и для первого способа, Aerospace.
Для анализа данных можно отображать несколько С-сканов одновременно. С помощью вида CCA (рис. 12) С-скан 1, построенный по сигналам из измерительного строба 1, и С-скан 2, построенный по сигналам из строба 2, можно отобразить один под другим и выявить различия в них для определения типа дефектов. Области, в которых амплитуда донного сигнала мала и нет сигналов от дефектов, являются областями микропористости. Координаты данных и измерения для текущей точки отображаются над каждым C-сканом.

Рис. 13. C-скан внутренних дефектов с картой цветов допустимо/недопустимо.
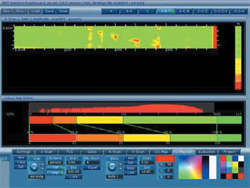
Рис. 14. C-скан и настройка новой карты цветов для определения степени пористости.

Рис. 15. Контроль разнотолщинности.
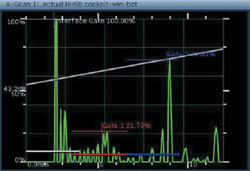
Рис. 16. A-скан хорошей склейки.
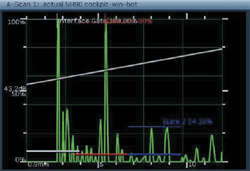
Рис. 17. А-скан частичного непроклея.
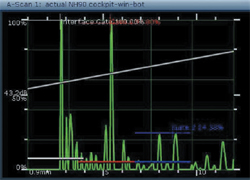
Рис. 18. A-скан полного непроклея.
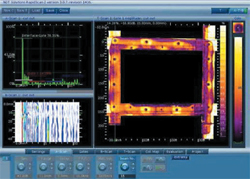
Рис. 19. T-скан с началом координат, смещенных на верхнюю левую заклепку.
Стандартные критерии годности основываются на разности уровней сигналов в децибелах (дБ) относительно «хорошей» области объекта. Во втором способе контроля внутренние дефекты определяются как любой сигнал, появляющийся между сигналами от поверхности ввода и донной поверхности, который на 6 дБ ниже амплитуды донного сигнала из «хорошей» области. Усиление было выбрано таким, чтобы сигнал из «хорошей» области составлял 80 % высоты экрана. По этой причине уровень спада 6 дБ можно аппроксимировать до 40 % высоты экрана.
C-скан 2 для поиска дефектов по отражению (абсолютная амплитуда строба 2) был повторно обработан как допустимый/недопустимый с пороговым значением годности, равным 40 % высоты экрана (рис. 13).
Другие критерии годности, связанные с уменьшением амплитуды донного сигнала, разделяют пористость по ее степени. Для этого была создана новая карта цветов Porosity с помощью редактора карт. Пористость разделена на четыре группы по затуханию сигнала: 0–6 дБ, 6–12 дБ, 12–18 дБ и более 18 дБ. Карта содержит 4 блока, которые были раскрашены следующим образом: ниже диапазона (черный), блок 1 (красный), блок 2 (оранжевый), блок 3 (желтый), блок 4 (светло-зеленый), над диапазоном (зеленый). Пределы были установлены таким образом, чтобы блок 4 соответствовал амплитуде 50–100 % (уменьшение амплитуды на 0–6 дБ); блок 3 соответствовал амплитуде 25–50 % (уменьшение на 6–12 дБ); блок 2 соответствовал амплитуде 12,5–25 % (уменьшение на 12–18 дБ); блок 1 соответствовал амплитуде 0–12,5 % (уменьшение амплитуды более чем на 18 дБ) (рис. 14).
Для анализа пористости измеряем площадь дефектов способом для контроля расслоения. Диапазон критериев годности может зависеть от таких факторов, как: конструкционная ответственность объекта, его толщина, расположение слов волокон, использованная смола и т.д.
Данный образец интересен еще и тем, что его толщина не постоянна, а изменяется. Для приведенного примера была использована карта цветов Spectrum: 0 мм (красный) – 8 мм (синий). Измерения проводятся по времени прихода донного сигнала относительно интерфейсного сигнала (рис. 15).
Контроль клеевых соединений
Этот пример демонстрирует использование дефектоскопа RS 2 WP для контроля поверхностей склеивания между композитными деталями на предмет расслоений и больших пустот.
В качестве образца была взята решетка из склеенного углепластика с толщиной элементов около 3 мм. Скорость звука в материале 3200 м/с. Необходимо выявлять нарушения склейки диаметром более 10 мм. Частота преобразователя 5 МГц.
Два измерительных строба настраиваются таким образом, чтобы на мониторе получить два С-скана: по сигналам от поверхности склеивания и от донной поверхности.
При хорошей склейке материала появляется сильное отражение от донной поверхности и лишь небольшое, если таковое вообще будет иметь место, с поверхности склеивания (рис. 16). При уменьшении процента проклеенной области под преобразователем (частичный непроклей) амплитуда сигнала с поверхности склеивания увеличивается, а амплитуда донного сигнала начинает уменьшаться (рис. 17). И, наконец, при отсутствии склейки сигнал полностью отражается от поверхности склеивания (полный непроклей) (рис. 18).
Для этого примера записываются поочередно четыре С-скана. Настройка цветовой палитры перед контролем проводится аналогично описанным выше примерам. Затем, пользуясь возможностью перемещения и вращения С-сканов, выполняется их «склейка» и формируется полное изображение ОК – Т-скан (рис. 19).
Заключение
Эффективность использования дефектоскопа RS 2 WP для контроля различных композиционных материалов, применяющихся в авиастроении, наглядно подтверждена примерами, описанными выше. Тестирование проводили на плоских образцах. Но также возможен контроль объектов другой формы и размеров, включая трубы, фланцы и наружные скругления, выполненных как из композитов, так и из различных металлических сплавов. Для каждого ОК требуется специальный преобразователь и своя методика контроля. Для настройки дефектоскопа RS 2 WP для УЗК необходимо иметь сведения о контролируемом объекте и о типовых дефектах, которые требуется в нем выявлять.
Ультразвуковая диагностическая система RS 2 WP показала результативную работу как на этапе отработки технологии изготовления изделий из ПКМ, так и при их производстве и эксплуатации.
На данный момент RS 2 WP внесен в Реестр средств измерений и допущен к применению на территории РФ.