Контроль газонефтепроводов
СПОСОБЫ ПОВЫШЕНИЯ ЭФФЕКТИВНОСТИ КОНТРОЛЯ ГАЗОНЕФТЕПРОВОДОВ С ИСПОЛЬЗОВАНИЕМ ТЕХНИЧЕСКИХ ВОЗМОЖНОСТЕЙ ДЕФЕКТОСКОПОВ SONATEST

Ультразвуковой дефектоскоп SONATEST 500S
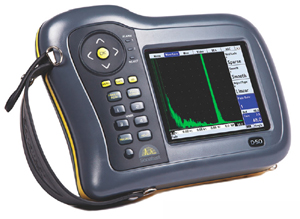
Ультразвуковой дефектоскоп SONATEST D-50
Дефектоскопию сварных соединений технологических и линейных частей (ЛЧ) магистральных газопроводов (МГ), а также магистральных нефтепроводов (МН) и стальных резервуаров хранения нефти (РВС) после их длительной эксплуатации, как правило, выполняют в соответствии с требованиями строительных норм. Способы выявления эксплуатационных дефектов, которые могут развиваться не только в сварном шве но и в основном материале изделий, а также проблемные вопросы контроля в процессе их длительной эксплуатации не рассматриваются в действующей эксплуатационной документации.
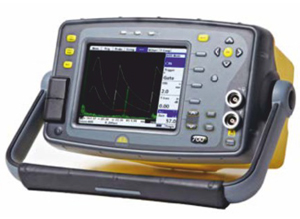
Ультразвуковой дефектоскоп SONATEST 700M
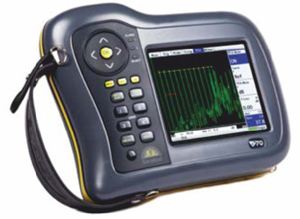
Ультразвуковой дефектоскоп SONATEST D-70
В эксплуатационной документации в основном приводятся технологии контроля, которые используются при строительстве новых трубопроводов. Применение таких технологий является необходимым, но не достаточным условием обнаружения эксплуатационных дефектов сварных соединений на объектах повышенной опасности.
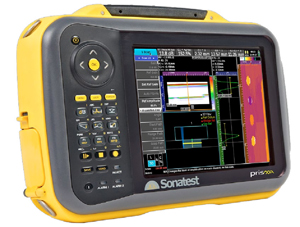
Ультразвуковой дефектоскоп HARFANG PRISMA UT
Рассмотрим основные проблемные вопросы контроля МГ, МН и РВС, которые необходимо обязательно учитывать в процессе их длительной эксплуатации.
- Низкое качество зачистки зоны перемещения УЗ преобразователя по изделию.
В закрытых помещениях газораспределительных станций (ГРС) зачистку трубопрорводов механическим способом, как правило, не выполняют, поскольку может произойти взрыв газа. Удаление защитных покрытий химическим способом не обеспечивает выполнение требований ГОСТ 14782 к качеству подготовки поверхности контролируемых изделий, что приводит к нарушению акустоконтакта.
- Обледенение контролируемого изделия.
В зимний период ультразвук может не возбуждаться в материале контролируемого шва, что приводит к пропуску опасных дефектов. На практике контроля сварных соединений технологических трубопроводов компессорных станций было установлено, что мешающим фактором является тонкий слой льда, который возникал в результате замерзания конденсата и совершенно не был виден глазом.
- Стыковые сварные соединения трубопроводов могут иметь провисания наплавленного металла в корне шва. Такие «сосульки», как правило, располагаются в потолочной части свариваемых трубопроводов и отражают ультразвук аналогично трещинам, которые располагаются в корне шва.
- Экономическая нецелесообразность удаления дорогостоящего защитного эпоксидно-полиамидного покрытия с поверхностей крупногабаритных изделий, например, на резервуарах вертикальных стальных типа РВС. Толщина защитного покрытия на указанных изделиях составляла 300 …600 мкм.
Все указанные проблемы могут быть решены способом слежения и автоматической корректировки чувствительности контроля при случайных изменениях акустоконтакта.
Во всех моделях ультразвуковых дефектоскопов компании Sonatest (таких как ультразвуковой дефектоскоп SONATEST 700, ультразвуковой дефектоскоп SONATEST D70, ультразвуковой дефектоскоп HARFANG PRISMA UT, ультразвуковой дефектоскоп SONATEST 500 и ультразвуковой дефектоскоп SONATEST D50) предусмотрена функция автоматической регулировки усиления (АРУ) сигнала акустоконтакта. Применение специализированных ультразвуковых преобразователей обеспечивает слежение за сигналом акустоконтакта (эхо-сигнала от внутренней поверхности изделия). Включение режима АРУ сигнала акустоконтакта, расположенного в стробе 1, обеспечивает автоматическую корректировку чувствительности в стробе 2 (рис.1), при условии отсутствия в основном материале ликваций, расслоений и т.п.
.jpg)
Применение режима АРУ с большим диапазоном регулировки усиления приемного тракта обеспечило выполнение УЗК стыковых сварных соединений РВС без удаления защитного покрытия толщиной 300…600 мкм. Такое покрытие, как правило, имело хорошую адгезию с материалом резервуара. На отдельных участках контролируемого изделия, где отсутствовал сигнал акустоконтакта, выполнялось удаление поврежденного защитного покрытия и последующий УЗК и МПК.
АРУ обеспечивает также УЗК сварных соединений трубопроводов через три слоя гидроизоляции (суммарной толщиной 300 мкм), с сохранением браковочного уровня чувствительности, установленного для зачищенных поверхностей трубопроводов.
При контроле прибором Sonatest, работающем в режиме АРУ, стыковых сварных соединений технологических трубопроводов ГРС без удаления лакокрасочного покрытия толщиной до 200 мкм были обнаружены трещины вдоль оси трубы, наличие которых подтверждено дублирующим МПК локальной зоны. Приведенные примеры свидетельствуют о существенных преимуществах приборов фирмы Sonatest, имеющих фенкцию АРУ, а также о необходимости применения дублирующих методов контроля для повышения достоверности результатов.
Применение в преобразователе раздельной схемы «тандем» обеспечивает «распознавание» шва с трещиной и шва с провисанием. Сигнал, отраженный от провисания, не приходит на приемный пьезоэлемент и поэтому не наблюдается на экране дефектоскопа (рис.1,а). Импульс, последовательно отраженный от трещины и донной поверхности трубопровода, приходит на приемный пьезоелемент и виден на экране в стробе 2 (рис.1,б).
АРУ сигнала акустоконтакта позволяет также компенсировать влияние следующих мешающих факторов:
- отличий в чистоте обработки поверхностей СОПа и контролируемого изделия;
- отличий в чистоте обработки поверхностей различных участков контролируемого изделия;
- различий в затухании ультразвука в СОПе и в контролируемом изделии, при условии равенства их толщин; такие различия при контроле технологических трубопроводов достигали значения 20 дБ;
- различий в усилии прижатия преобразователя к поверхностям СОПа и изделия;
- случайные изменения усилия прижатия УЗ преобразовагеля к поверхности контролируемого изделия;
- случайные изменения степени загрязненности контактной среды.
Технические возможности дефектоскопов компании Sonatest обеспечивают устранение указанных мешающих факторов, а также обладают широким рядам других отличительных возможностей:
- режим автоматического расчета и построения АРД- диаграмм для оценки размеров дефектов в процессе контроля толстостенных деталей;
- удобство построения кривых ВРЧ и ДАК;
- возможность работы при температурах от -20°С до + 70°С;
- полностью русифицированное меню.
Ультразвуковые дефектоскопы компании Sonatest внесены в реестр РосСтандарта и могут быть применены на объектах повышенной опасности.
Какие виды дефектов следует учитывать при отработке эксплуатационной документации
При длительной эксплуатации ЛЧ МГ и МН в трубопроводах чаще всего появляются стресс-коррозионные трещины, которые ориентируются вдоль оси трубопровода (поперек оси кольцевого шва) и располагаются в околошовной зоне сварного соединения или в основном материале (рис. 2).
.jpg)
Такие трещины чаще всего образуются на наружной поверхности трубопровода в результате отслоения защитного гидроизоляционного покрытия и последующего заполнения образовавшегося зазора (трубопровод-гидроизоляция) коррозионной средой под действием капиллярных сил.
При длительной эксплуатации ЛЧ МН в нижней части внутренней поверхности трубопровода может дополнительно возникать так называемая «ручейковая коррозия», которая также ориентирована вдоль оси трубопровода.
При ультразвуковом контроле кольцевого сварного соединения по технологии, приведенной в ВСН 012-88, такие эксплуатационные дефекты не выявятся, поскольку они ориентированы вдоль направления прозвучивания (рис. 3).
Для обнаружения таких дефектов необходимо направить ультразвук не перпендикулярно, а вдоль оси кольцевого сварного соединения (рис. 4).
.jpg)
В околошовной зоне сварного соединения брызги металла могут отражать ультразвук аналогично поверхностным трещинам, что затрудняет принятие решения о техническом состоянии трубопровода. Для распознавания характера отражателя целесообразно проведение дублирующего магнитопорошкового контроля (МПК) в приложенном магнитном поле с использованием постоянных магнитов WM-5C (производства Western Instuments Inc.). Применение такого способа МПК позволяет также визуализировать трещины, которые развиваются с внутренней поверхности трубопровода, толщина стенки которого не превышает 10 мм.
Стыковые сварные соединения трубопроводов могут иметь внутренние металлургические дефекты основного материала – ликвационные зоны или расслоения, которые ориентированы вдоль поверхности трубопровода. Такие зоны практически исключают возможность выявления дефектов сварного шва наклонными преобразователями (рис. 5).
.jpg)
Для оценки контролепригодности сварного соединения необходимо на этапе подготовки к контролю выполнить прозвучивание околошовной зоны прямым УЗ преобразователем, в пределах выбранной зоны перемещения наклонного УЗ преобразователя (рис. 5). Указанное требование изложено в п. 2.3 ГОСТ 14782-86. Однако на оценку контролепригодности сварного соединения, как правило, не обращают внимания при разработке эксплуатационной и нормативно-технической документации.
При УЗК основного материала прямым УЗ преобразователем и отсутствии ликвационных зон, на экране прибора наблюдается донный эхо-импульс (рис. 6,а). При наличии в основном материале ликвационных зон, дополнительно наблюдаются промежуточные эхо-импульсы (рис. 6,б), амплитуда и количество которых скачкообразно изменяются при незначительных перемещениях прямого УЗ преобразователя.
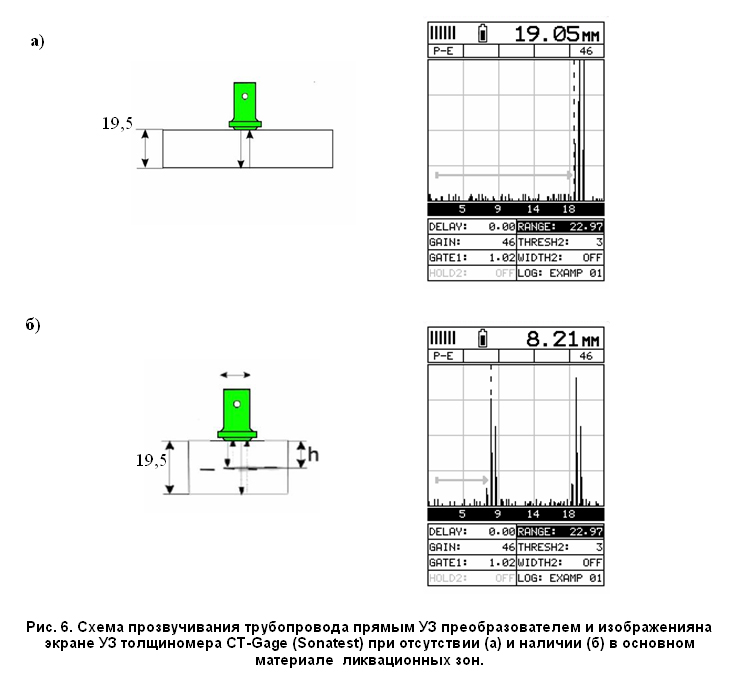
При работе с УЗ толщиномерами без экрана и наличии ликваций, прибор показывает не значение толщины стенки трубопровода, а расстояние до ликваций. Это обусловлено тем, что такие УЗ толщиномеры автоматически рассчитывают толщину стенки по первому принимаемому эхо-импульсу, что многие специалисты, как правило, не знают. Поэтому для предотвращения ошибочного определения толщины стенки трубопровода необходимо использовать УЗ толщиномеры с экраном (например, CT-Gage) или УЗ дефектоскопы, которые всегда имеют экран.
В практике внутритрубной УЗ толщинометрии дефектоскопом-снарядом ЛЧ МГ и МН имелись случаи забракования отремонтированного участка трубопровода (вваривалась новая труба) по наличию в основном материале ликвационных зон.
Если ликвационные зоны располагаются у торца новой трубы, то в процессе ремонта сваркой труба может расслаиваться по ликвационным зонам, что практически исключает возможность ремонта участка трубопровода.
Для исключения подобных случаев необходимо выполнять УЗ толщинометрию новых труб до начала ремонта.
Выявленные на практике проблемы и особенности неразрушающего контроля изделий при их эксплуатации целесообразно учитывать в процессе разработки эксплуатационной, нормативно-технической документации и обучения персонала. Исследованиями влияния всего разнообразия дефектоскопических характеристик на достоверность результатов УЗК сварных соединений авторы статьи не занимались.
ЛИТЕРАТУРА:
1. ВСН 012-88. Строительство магистральных и промысловых трубопроводов. Контроль качества и приемка работ. Часть 1. М., 1989.
2. ГОСТ 14782-86. Контроль неразрушающий. Соединения сварные. Методы ультразвуковые. М.: Стандарты, 1987.
Купить ультразвуковые дефектоскопы и толщиномеры, предварительно ознакомившись с их работой, Вы можете в ООО «ПАНАТЕСТ». Наши квалифицированные специалисты обеспечивают качественное гарантийное и постгарантийное обслуживание приборов.
Обращайтесь по телефонам: +7 (495) 918-09-30, 362-78-73, 673-02-23. Менеджеры компании оперативно ответят на любой Ваш вопрос. г. Москва, ул. Авиамоторная 12, офис 405; Тел./факс: +7 (495) 789-37-48, +7 (495) 587-82-98.