Контроль композитных материалов
КОМПЛЕКСНЫЙ ПОДХОД К ВЫЯВЛЕНИЮ ДЕФЕКТОВ МНОГОСЛОЙНЫХ КОНСТРУКЦИЙ ИЗ КОМПОЗИТНЫХ МАТЕРИАЛОВ
Представлены экспериментальные результаты применения современных тепловизионных систем серии ТН-9100 и ультразвуковых импульсных дефектоскопов серии SONATEST 700 для выявления дефектов в конструкциях из композиционных материалов, используемых в авиационной промышленности и технике.
В процессе отработки технологии и изготовления крупногабаритных изделий из композиционных материалов возникает необходимость проведения оперативного контроля значительных площадей конструкций, с последующим уточнением параметров выявленных дефектов (размера, глубины залегания и формы).
В данной работе рассмотрены возможности применения методов ИК-термографии и ультразвукового метода контроля для решения рассматриваемой проблемы.
В последние годы методы ИК-термографии рассматриваются как одно из перспективных направлений в технике неразрушающих испытаний изделий, в том числе и конструкций из композиционных материалов [1]. Практическое применение методов ИК-термографии в ряде случае затруднено и связано с необходимостью использования опытных специалистов для интерпретации результатов контроля и их анализа. В ряде работ рассмотрена возможность передачи функций анализа температурной информации и автоматизированного обнаружения дефектов, используя достаточно сложные алгоритмы теории распознавания образов [2]. Данные направления работ представляют значительный интерес, однако в настоящее время не вышли за рамки лабораторных исследований.
Для выявления признаков наличия дефекта методом ИК-термографии необходимо выяснить может ли временное изменение температуры быть описано одномерным приближением для однородной среды или нет. Это позволяет провести упрощенный анализ и выявить признаки наличия дефектов по кривой изменения температур.
Кривая временного изменения температуры при наличии дефектов типа включений или расслоений с воздушными промежутками располагается выше кривой охлаждения изделия без дефектов [3]. Для включений с повышенной теплоемкостью, например, при увлажнении полостей расслоений, кривая временной зависимости охлаждения образца будет располагаться ниже кривой охлаждения образца в бездефектной зоне (рис 1).
Рис.1.
Кривые охлаждения в зонах бездефектного (2) и дефектных (1,3)
участков.
Как видно из графиков, разность температур поверхности над дефектом, по сравнению с бездефектным участком, на начальном временном периоде увеличивается, а затем уменьшается. Как правило, превышение температуры для определенной глубины залегания дефекта имеет максимум или минимум для включений с отличными от основного материала теплофизическими свойствами.
В области регулярного (установившегося) теплообмена, изменение температуры в двойных логарифмических координатах описывается линейной функцией. Для бездефектной области функция временного изменения температуры описывается линейной функцией с фиксированным отрицательным углом наклона, что следует из решения нестационарного уравнения теплопроводности для однородного полупространства. Наличие дефекта изменяет скорость распространения тепловой волны так, что при наблюдении за температурой на поверхности изделия, дефекты обнаруживаются в виде зон с отличающейся (относительно бездефектных областей) температурой. Глубоко расположенные дефекты наблюдаются с большей задержкой по времени и уменьшенным температурным контрастом.
Время от начала импульсного воздействия до обнаружения температурной аномалии пропорционально квадрату глубины залегания дефекта. Абсолютная величина температурного контраста изменяется во времени ипримерно обратно пропорциональна кубу глубины расположения дефекта от поверхности облучения и контроля. Длительность наблюдения проявления дефекта от начала температурного переходного процесса пропорциональна квадрату глубины залегания дефекта и обратно пропорциональна коэффициенту α температуропрводности материала [4].
Для типичных композитных пластиковых материалов значение α ≈1·10-7м2/с (органопластики) и α ≈5·10-7м2/с (углепластики). Признаки расслоений с характерным размером, сопоставимым с глубиной залегания, обнаруживаются сравнительно легко при обеспечении необходимого импульсного энергетического воздействия на поверхность объекта контроля, или при остывании предварительно нагретого объекта в атмосфере.
В данной работе исследования проводились на стеклопластиковых и углестеклопластиковых многослойных образцах толщиной 5…10мм, в которых были выполнены искусственные дефекты, ориентированные параллельно поверхности, так и фрагментов натурных конструкций с естественными технологическими дефектами типа расслоений. Диаметр искусственных дефектов в указанных образцах составлял от 3 до 20 мм. Глубина залегания дефектов составляла от 1 до 5 мм.
В опытах использован тепловизор серии ТН-9100 фирмы NEC (Япония), с температурным разрешением ~0,05К. и ультразвуковой импульсный дефектоскоп типа SONATEST 700 фирмы Sonatest (Великобритания).
Термограммы процесса остывания объекта получены в режиме отрицательного теплового воздействия (остывания предварительно равномерно нагретого фрагмента объекта в свободной атмосфере). Подобное тепловое воздействие наиболее близко моделирует тепловой переходный процесс в технологическом процессе изготовления изделий. Характерные термограммы процесса свободного остывания фрагмента изделия из углестеклопластика приведены на рис.2, а из стеклопластика - на рис. 3.
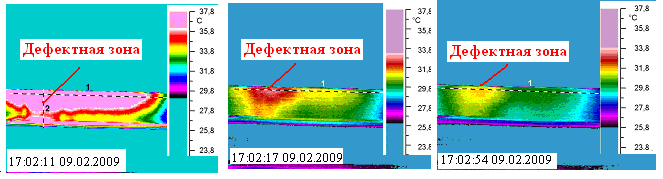
Рис.2. Термограммы фрагмента конструкции из углестеклопластика. Область выявленного расслоения показана стрелкой.
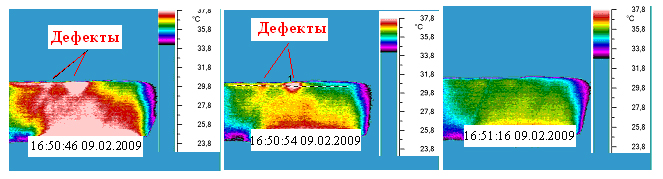
Рис. 3. Термограммы процесса остывания изделия из стеклопластика. Области выявленных расслоений показаны стрелками.
Как видно из приведенных термограмм, дефекты надежно обнаруживаются без привлечения сложных методов обработки тепловых изображений. Из термограмм следует, что превышение температуры поверхности (в области максимального контраста) достигает ΔТ= 4°С, что более чем на порядок превышает предел температурного разрешения используемой тепловизионной системы.
К достоинствам описанного подхода следует отнести возможность осуществления оперативного контроля состояния протяженных поверхностей в ходе технологического процесса в тех случаях, когда имеют место переходные тепловые режимы.
Наряду с описанными преимуществами термографический метод контроля не свободен от недостатков, главным из которых является требование обеспечения оптического доступа к поверхности объекта, а также обеспечение однородности излучательных свойств и начальной температуры контролируемой поверхности. В ряде случаев отмеченные особенности можно преодолеть путем применения дифференциального анализа термограмм, а также применения дублирующих методов контроля, например, ультразвукового метода.
Ультразвуковой контроль локализованных термографическим методом зон выполнялся ультразвуковым дефектоскопом SONATEST 700, работающим в эхо-импульсном режиме на частоте 1 МГц, с применением прямого преобразователя раздельно-совмещенного типа. Для одновременного наблюдения дефектов (расслоений) по толщине контролируемого изделия, а также за качеством акустического контакта преобразователя, в ультразвуковом дефектоскопе SONATEST 700 предусмотрено выделение временных строб-импульсов. Это обеспечивает выдачу сигнализации при появлении эхо-сигналов от дефектов в области первого строба, так и нарушение акустического контакта при пропадании донного импульса в область второго строба.
Основной задачей ультразвукового контроля являлось подтверждение результатов обнаружения дефектов термографическим методом, а также точное определение глубины залегания расслоений. Данный вид контроля предполагается использовать при осуществлении технологического процесса изготовления конструкций из многослойных композитных материалов.
Типичные изображения на экране дефектоскопа, полученные в бездефектной и дефектной зонах конструкции, приведены на рис. 4. Горизонтальные стробирующие сигналы 1 и 2, изображенные на экране ультразвукового дефектоскопа SONATEST 700 (рис 4 и рис.5), показывают области потенциального расположения дефекта (зона контроля) и донного эхо-сигнала для контроля качества акустического контакта.
Рис. 4.
Изображение на экране дефектоскопа SONATEST 700:
а)- бездефектная
зона изделия из композиционного углестеклопластикового
материала; б)-дефектная зона изделия.
При наличии в дефектной зоне небольших по площади дефектов (непроклеев), расположенных на разной глубине (рис. 5,а), наряду с эхо-сигналами от дефектов отображается также донный эхо-сигнал.
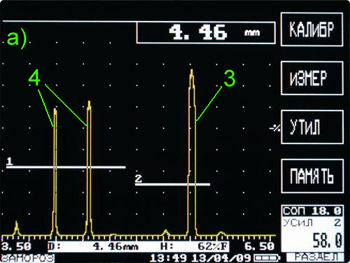

Рис. 5. а) -
отображение двух небольших по площади расслоений материала;
б)- дефекты
увеличенной площади: 1, 2 – строб-импульсы; 3- донный сигнал; 4-эхо- сигналы от
дефектов.
С увеличением площади непроклея пропадает донный сигнал и наблюдаются только эхо-сигналы от непроклеев (рис. 5 б). Следует отметить, что при отсутствии акустического контакта ультразвукового преобразователя с контролируемым изделием, все эхо-сигналы отсутствуют.
Макрошлиф
дефектного участка, выявленного термографическим и подтвержденного
ультразвуковым эхо-импульсным методами в конструкции из композиционного
стеклопластикового материала, приведен на рис.6.
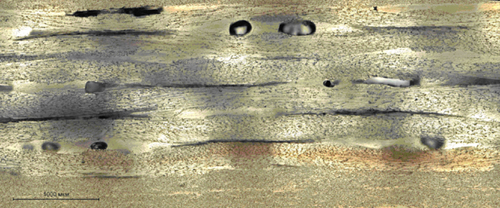
Рис. 6. Макрошлиф дефектного участка конструкции из стеклопластика, выявленного термографическим и ультразвуковым методами контроля.
В результате исследований установлено, что эхо-импульсный ультразвуковой метод контроля ультразвуковым дефектоскопом SONATEST 700 многослойных конструкций на основе стекло- и угле-пластиковых композитных материалов обеспечивает обнаружение более меньших по площади дефектов (расслоений, непроклеев), в сравнению с тепловым и теневым ультразвуковым методами контроля. Как и тепловой метод, ультразвуковой эхо- метод не требует двустороннего доступа к контролируемому объекту, что часто реализуется на практике.
Таким образом, полученные результаты показывают на перспективность применения комбинированного подхода к контролю, сочетающего возможности оперативного контроля значительных площадей объекта термографическим методом, с последующим уточнением параметров выявленных дефектов (размера, глубины залегания и формы) ультразвуковым эхо-импульсным методом.
Тепловизоры
серии ТН-9100 и ультразуковые импульсные дефектоскопы типа SONATEST 700
по своим техническим характеристикам позволяют обеспечить возможность
достоверного обнаружение непроклеев и расслоений, при относительно низкой
трудоемкости контроля крупногабаритных композиционных изделий, подобных лопастям
вертолетных винтов и др.
ВЫВОДЫ
Предложенный в работе подход, основанный на использовании нескольких методов диагностики, эффективен для дефектоскопии изделий непосредственно в ходе технологической цепи их производства, где требуется оперативная локализация наличия дефектных участков (непроклеев, расслоений). Определение основных характеристик дефектов (размера и глубины залегания) может быть произведено ультразвуковым методом локации. Необходимость решения указанных задач подобной постановки возникает как на этапе отработки технологии изготовления изделий, так и проведении стендовых испытаний конструкций. Близкие по характеру задачи связаны с обнаружением образовавшихся дефектов и увлажнений композиционных и сотовых конструкций в процессе эксплуатации авиационной техники.
Предварительная проработка методических аспектов контроля, с учетом технологических особенностей изготовления изделий, является необходимым атрибутом успешного использования применяемых средств дефектоскопии.
ЛИТЕРАТУРА:
1. Вавилов В.П. Тепловые методы неразрушающего контроля. М.:, «Машиностроение» 1991, 240 с.
2. N P Avdelidis, A Moropoulou, Z P Marioli-Riga, “Invited Paper: The technology of composite patches and their structural reliability inspection using infrared imaging”, Journal of Progress in Aerospace Sciences, Vol. 39, No 4, pp 317-328, 2003.
3. D Bates, G Smith, D Lu, J Hewitt, “Rapid thermal non-destructive testing of aircraft components”, Journal of Composites Part B: Engineering, Vol. 31, No 3, pp 175-185, 2000.
4. D.A. González, C. Ibarra-Castanedo, M. Pilla, M. Klein, J.M. López-Higuera, X. Maldague, Automatic Interpolated Differentiated Absolute Contrast Algorithm for the Analysis of Pulsed Thermographic Sequences, Proceedings of 7th International Conference on Quantitative Infrared Thermography (QIRT’04), 2004
Купить ультразвуковые дефектоскопы и толщиномеры, предварительно ознакомившись с их работой, Вы можете в ООО «ПАНАТЕСТ». Наши квалифицированные специалисты обеспечивают качественное гарантийное и постгарантийное обслуживание приборов.
Обращайтесь по телефонам: +7 (495) 918-09-30, 362-78-73, 673-02-23. Менеджеры компании оперативно ответят на любой Ваш вопрос. г. Москва, ул. Авиамоторная 12, офис 405; Тел./факс: +7 (495) 789-37-48, +7 (495) 587-82-98.